Kuiken Brothers’ KB Classical Moulding and Modern Craftsman Moulding collections are milled from Appalachian Poplar, double primed and buffed. Many of the larger profiles are milled from blanks that use a horizontally joined finger joint (FJ) product. This joint is also known as an “American Style” joint which differs from a vertical or “European Style” joint in that the fingers are only visible from the edge of the product and become virtually invisible to the eye and touch once our factory applied double primed and buff process is completed. This process results in a joint that is essentially as strong as the wood fiber itself.
Below are the features & benefits of milling from an American style engineered Appalachian Poplar block:
- Allows us to supply you with premium 16′ lengths
- Significantly reducing waste and overage charges
- In general, poplar mills to an extremely smooth surface, providing sharp and crisp edges, essential for the elegant designs of the Classical & Modern Craftsman moulding collections
- Poplar is the preferred species for a paint grade moulding
- Poplar is non-resinous (non-bleeding)
You can learn more about the American style engineered process below.
Above is an example of the fingers that are cut into each “block” before a finger joint blank is created. Precision ground, high-speed steel knives are used to cut the fingers into each block that is used and quality checks are performed every hour on multiple joints per blank to ensure a uniform and strong joint with no gaps. Because all knots and imperfections are removed, the individual finger joint blocks range between 6″ and 24″, so in any of our 16′ long KB Classical Moulding profiles, there can be anywhere between 8 and 32 total finger joint blocks.
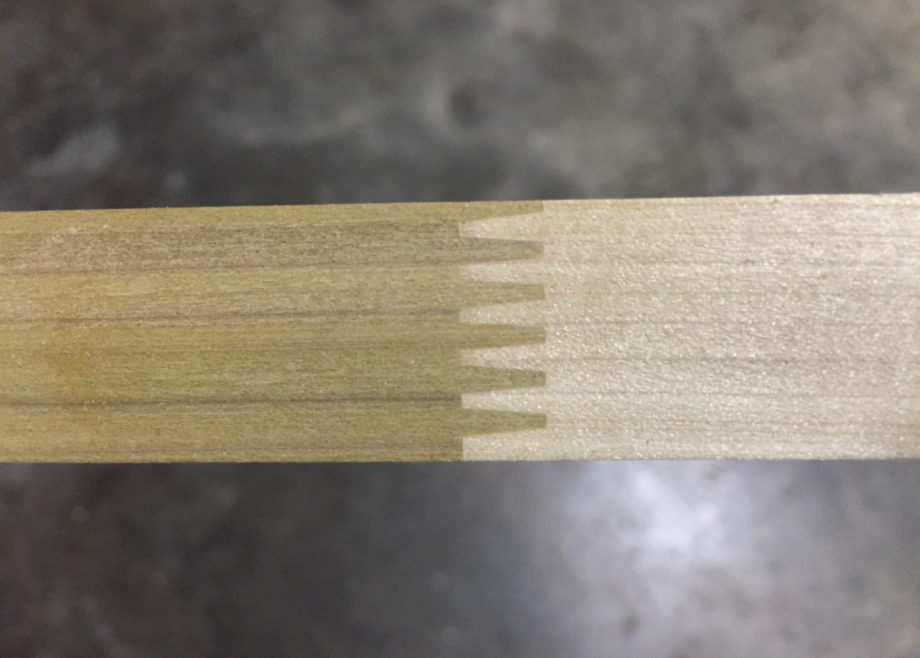
Color variation is a natural occurrence in poplar, but since it is a non-resinous (non-bleeding) species, there is no risk of bleed that may occasionally occur in some mouldings milled from pine. Once our factory applied double prime and buff is applied, the color variation is no longer visible.
Once the fingers are cut, a vinyl acetate based glue is applied to the joint (1 hour cure time) and they are mechanically pressed to form a seamless blank. The finger joint product line is equipped with a glue detection system which scans each block to ensure proper glue application – any rejected blocks are immediately removed from the assembly line prior to moulding. The resulting joint is essentially as strong as the fiber itself. Each block is trimmed to a true square before the fingers are cut, resulting in a very straight blank. At this point, the blank is ready to begin the moulding process. The video below shows the making of our KB138 Georgian casing with it’s big, bold backband. Many of the casing profiles found within the Classical Moulding Collection are 1-13/16″ thick, with the KB123 casing coming in at a full 2″ thick.
Because of this precision manufacturing process, we are able to offer the clean lines and deep incisions required for the detailed patterns found within the KB Classical Moulding process. If you are interested in specifying Kuiken Brothers Moulding profiles for an upcoming project, or have already chosen the package of your desire, please feel free to give us a call (201) 652-1000 or complete our on-line Contact Form and a Kuiken Brothers representative will follow up with you right away. We look forward to working with you on your next project!
Kuiken Brothers offer a number of additional design resources for builders, remodelers, architects, designers and their clients:
- Moulding Design Guide
- On-Line Moulding Library
- Full Line Moulding Catalog
- Classical Moulding Catalog
- Millwork Showrooms
You can view a number of Classical Moulding Installations in the gallery below.